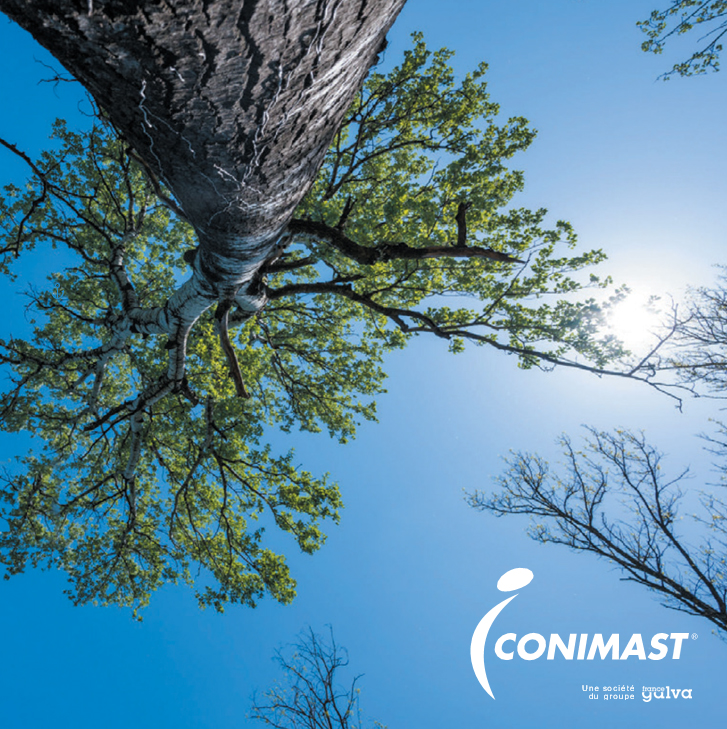
- It means choosing a company that is rooted in its local area, fully aware of its responsibilities and concerned about its environmental and economic ecosystems.
- It’s buying French
- It means working with one of the only French companies to integrate all manufacturing operations on a single site: from the steel coil to the mast delivered to your site.
Less transport, less transfer,
means less CO2!
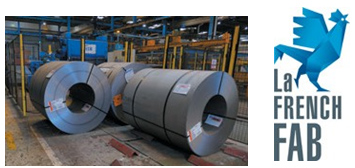
WE DON’T JUST PLANT TREES, WE TAKE ACTION!
A strategic choice underpinned by conviction
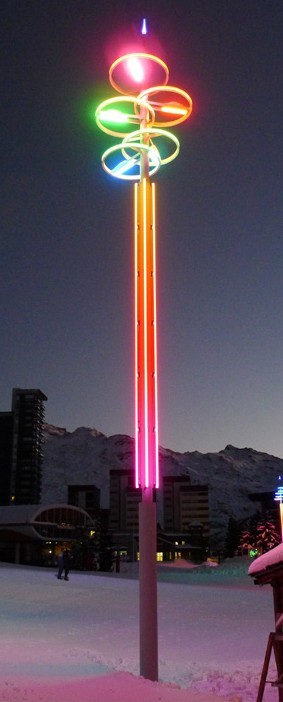
It’s easy to unburden yourself and buy a good conscience:
Offsetting carbon -> while -> not trying to combat its emissions
Subcontracting activities -> while -> not monitoring subcontractors
Buying rights to pollute -> while -> distorting competition
Shirking one’s responsibilities -> while -> manufacturing wherever standards are the least stringent
Reduce costs -> while -> buying at the lowest price
In a nutshell, subcontracting allows us to free ourselves from problems and responsibilities, and to present a green balance sheet at a lower cost.
For many years now, the France Galva Group has been implementing a continuous process of improvement in its environmental impact and rigorous compliance with current standards.
Each site, whether it employs 20 or 250 people, includes a Quality Safety Environment manager on its management team, to ensure that local issues are managed with the utmost care.
The head office support team is made up of 5 people.
Our standards:
These standards, along with total control over the production of candelabras, from sheet metal to mast, require us to adhere to the strictest ethical standards.
our mast production line
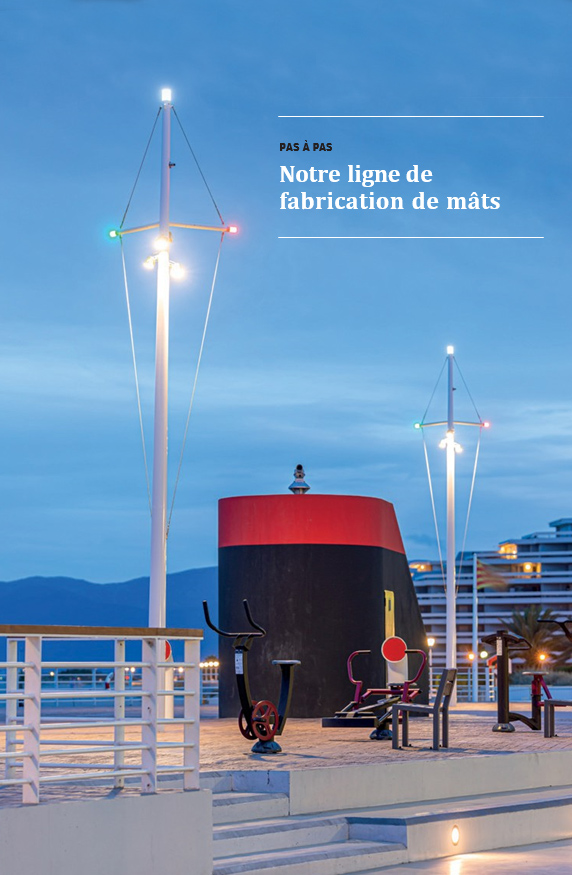
1. Steel coils
The steel comes from Arcelor Mittal or its French subsidiaries (sources: supplier rules and commitments).
2. peeling levelling
The use of superior S235 and HLE steels makes it possible to limit the weight of products by working on the thickness and conicity of masts for very demanding weights and wind zones.
3. slitting
Computer-aided design and drafting systems optimize dimensions to limit waste and scrap (profitability and price).
4. trapezius cut
Conimast is equipped with an automated line to remove the base and top slants of the masts to limit rework and scrap.
5. Bending / robotic line
Conimast is equipped with an automatic, robotized folding machine for greater repeatability and staff safety.
The company works with a number of recycling companies:
. For steel scraps
. For hydraulic oils
. For solvents
6. welding (Chrome 6 banned from process)
By bringing together and melting the metal without filler metal (plasma technology) or by bringing together and filler metal (submerged flux technology).
Welding rework.
Welding wire supplier: SAF – Air Liquide.